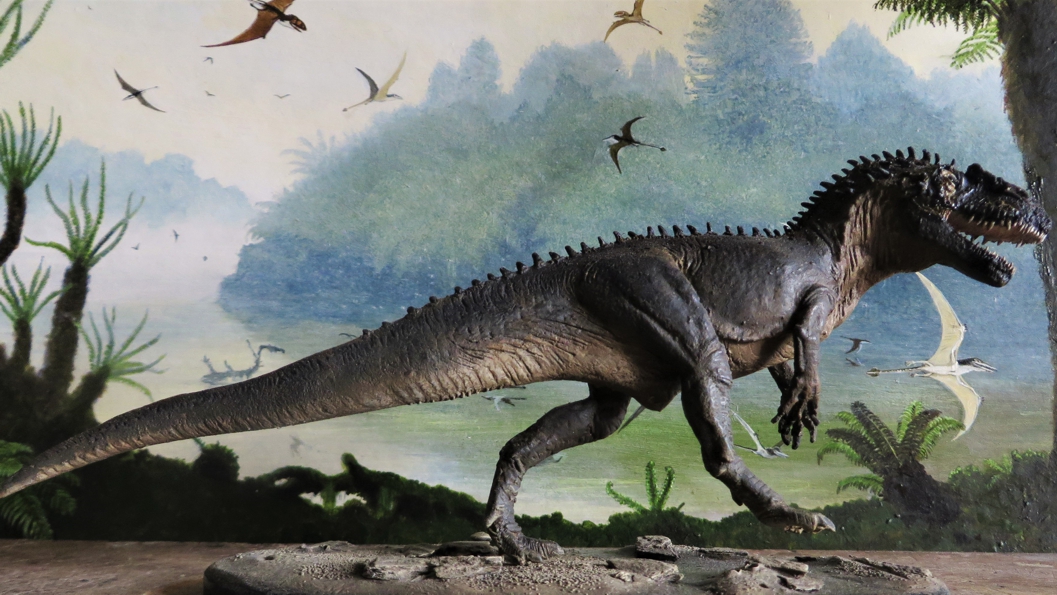
“Art and model making are really the only way those of us living in the present day might see dinosaurs and other long vanished animals as they were.” Those are the words of Andrew Treaner-Harvey, whose love of extinct creatures and desire to understand them has led to him creating a series of dinosaur models using Green Stuff.
Andrew is an artist and model maker from Cornwall and talking to him is rather fascinating. He spends hours sculpting and creating purely for his own enjoyment.
His model making does not really extend beyond that, although he does discuss with a friend down his local pub the most important matters of the day… namely, Airfix and how best to convert an existing figure into Tom Baker’s version of Doctor Who.
Today though, we are talking dinosaurs: “The animals are for nothing other than my own pleasure. I just love dinosaurs and any other long vanished animals,” says Andrew. “Apart from watching the birds in one’s garden, art and model making are really the only way we can see them as they once were.”
And our knowledge of what these magnificent creatures were is changing all the time. Something which model making and art can reflect better than most mediums; dinosaur models can be adapted and modified for accurate representations which update our impressions.
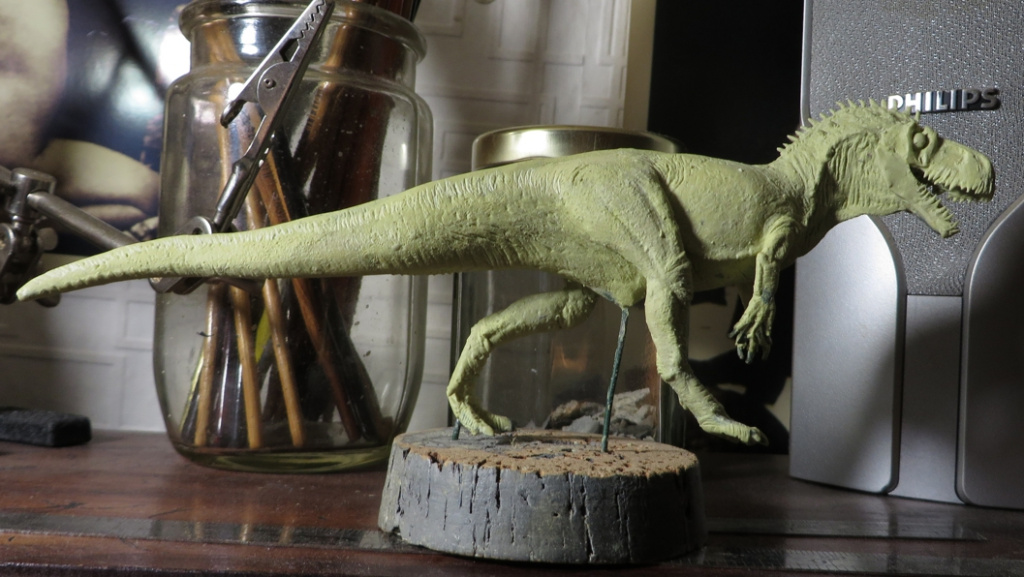
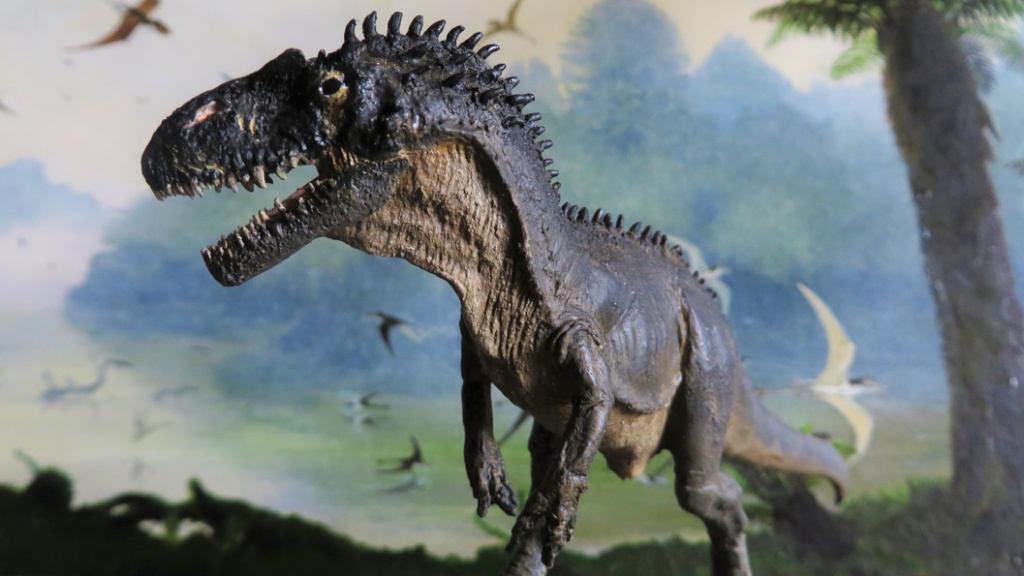
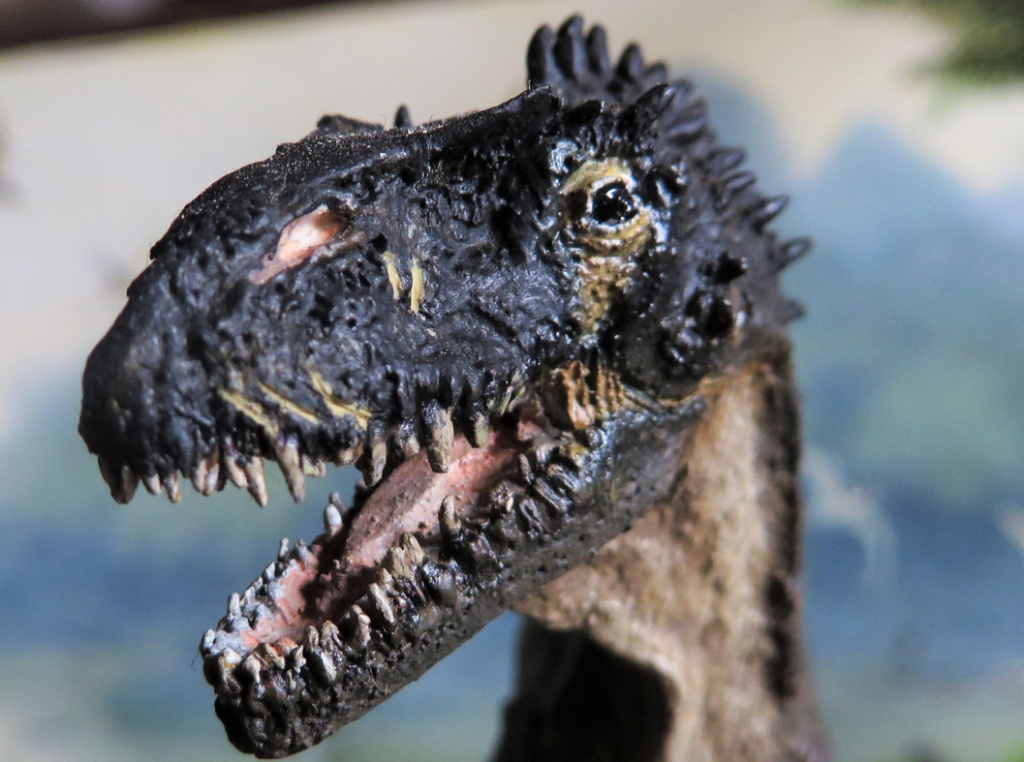
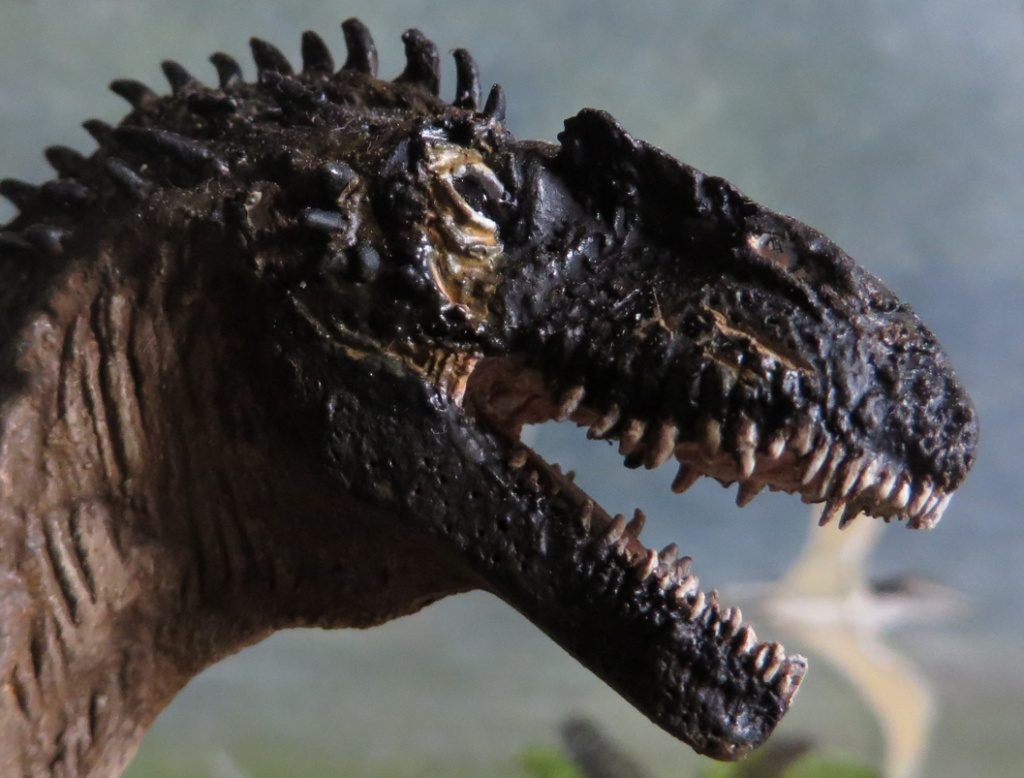
Take the famous Tyrannosaurus rex, for example. When you picture T. rex in your mind, do you imagine it with feathers? Because you should. T. rex is part of the tyrannosaur family and in 2004, another member was discovered in China.
Dilong paradoxus was the first tyrannosaur to be found with fossilised feathers. Subsequent studies and further discoveries over the past two decades mean scientists now believe that all tyrannosaurs came with feathers, including the T. rex.
A one-year-old T. rex would have been the size of a goose and covered in feathers. Not many of this apex predator made it beyond that age; they were small enough to be eaten by other carnivorous dinosaurs.
Those who did survive grew quickly, piling on 100 pounds a month or more whilst losing some of its plumage. But even by the time T. rex reached its 20s and was fully grown into a 9 ton beast, it would still have patches of feathers.
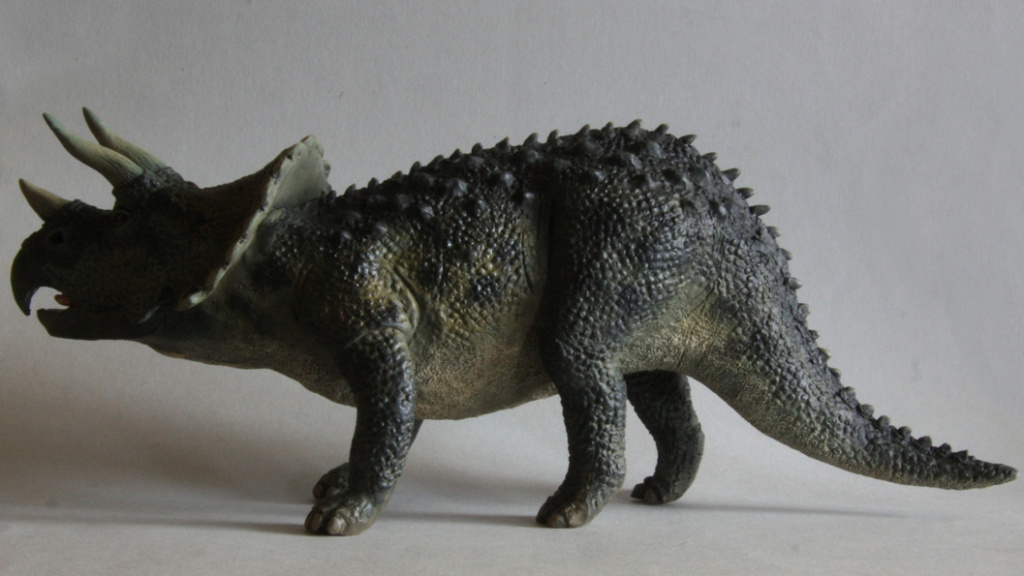
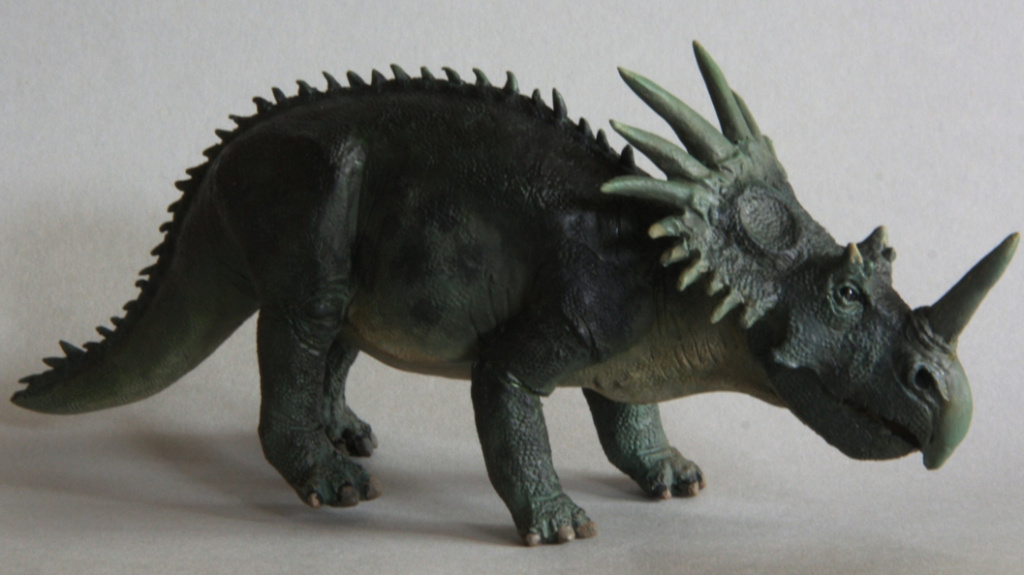
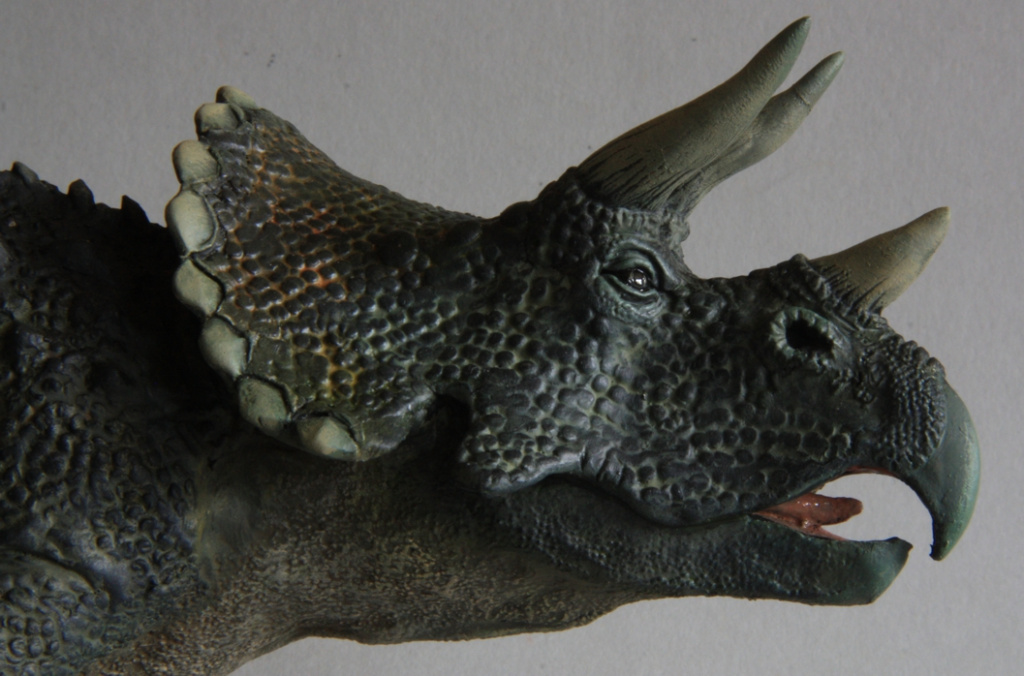
How about Velociraptor? Most people think of ‘raptors as a human-sized, lighting quick predator, thanks mainly to the way it is portrayed in the Jurassic Park franchise and the torment it causes Sam Neill and his Hollywood co-stars in the 1993 original film.
In reality, Velociraptor was barely half a metre high. Like Tyrannosaurus, it was also covered in feathers – something not discovered until 2007, 14 years after Steven Spielberg’s Oscar-winning epic brought Velociraptor into the hearts and nightmares of modern-day humanity.
Whereas Spielberg cannot go back and change the original Jurassic Park movie to reflect what we now know about T. rex and Velociraptor, Andrew is constantly creating new models so that his dinosaurs are as accurate as possible up to current knowledge.
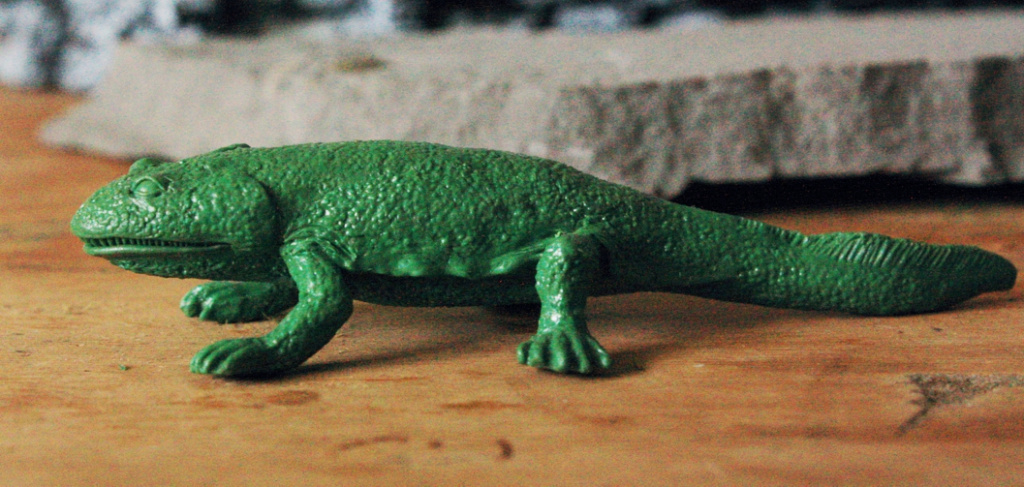
He studies closely Palaeontological papers, looks at pictures of fossils and reads up on a great deal of anatomical detail to get the animals just right. This desire for accuracy extends to his 1/48th scale human figures, including the aforementioned Tom Baker and other incarnations of Doctor Who.
“I do not really like the ‘heroic’ scales, with all the disproportionate heads and hands,” says Andrew. “I think it was John Blance of Citadel Miniatures who once wrote that an ordinary person shrunk down to the size of an inch would be a rather boring thing to look at.”
“Therefore, it was up to the artist or model maker to make things more exaggerated to add interest. He was right, but as I am only trying to please myself, I feel there is more of a challenge in getting things right anatomically. For me, one simply must get things right, and keep challenging one’s skills.”
“An Allosaurus I recently sculpted should be bang on with current knowledge. I worked the face out from a science paper that was published a couple of years ago. I still have it somewhere. Somebody did a superb illustration to show how the animal would have looked, and I have tried to be faithful to that.”
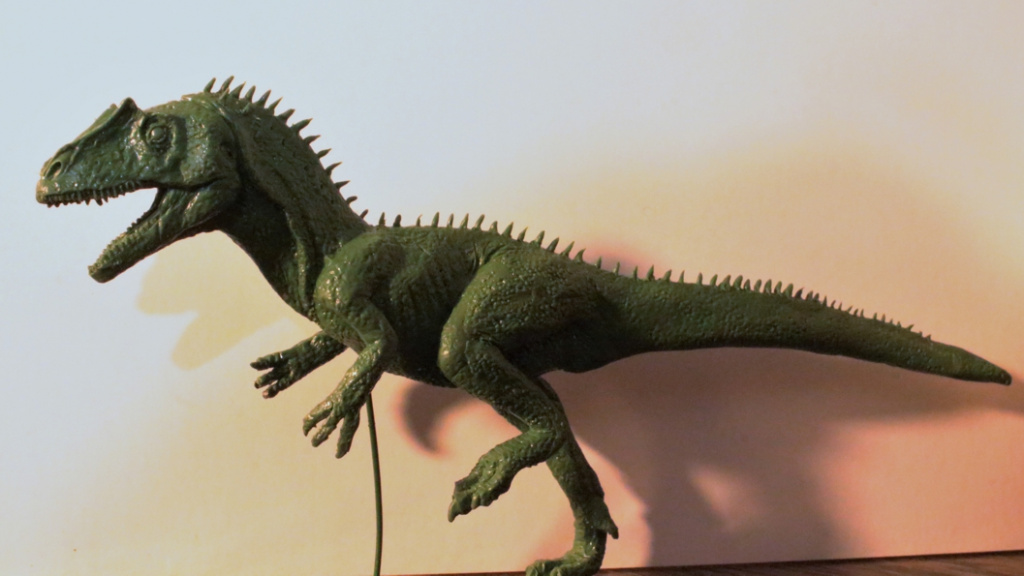
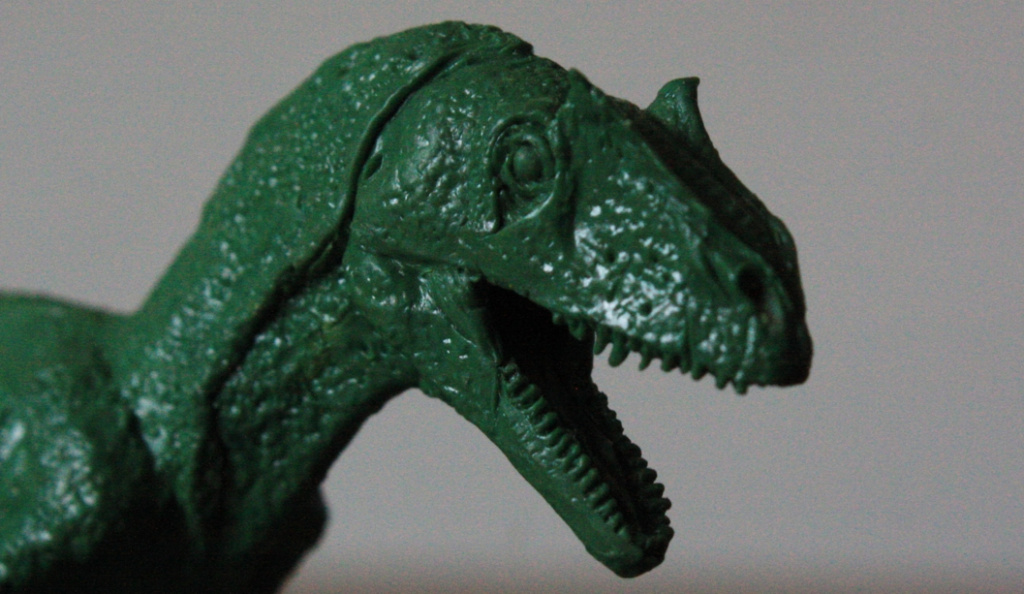
Andrew has even received help from experts in the field with his models, sketches and paintings: “I have a big oil painting of Stegosaurus awaiting its colours at present. I work in the old way which oils were first used for; black, burnt umber and white under painting, then colours in thin layers.”
“I contacted a palaeontologist some time ago and sent her some of my sketches of Stegosaurus. She said I was almost right, except the neck needed to be longer, but they hadn’t known that until recent new findings. That was encouraging.”
Through his dinosaur models, Andrew is producing a visual record of how our knowledge regarding the animals grows and develops. His most recent Stegosaurus might (nearly) have the seal of approval from an expert, but older efforts reflect the image we once had of one of the more well-known dinosaurs.
“Some of the model Stegosaurus I have made are of the ‘old school’ tail dragger type. These are based on the all the old paintings and illustrations of people like Zdenek Burain. I love his work.”
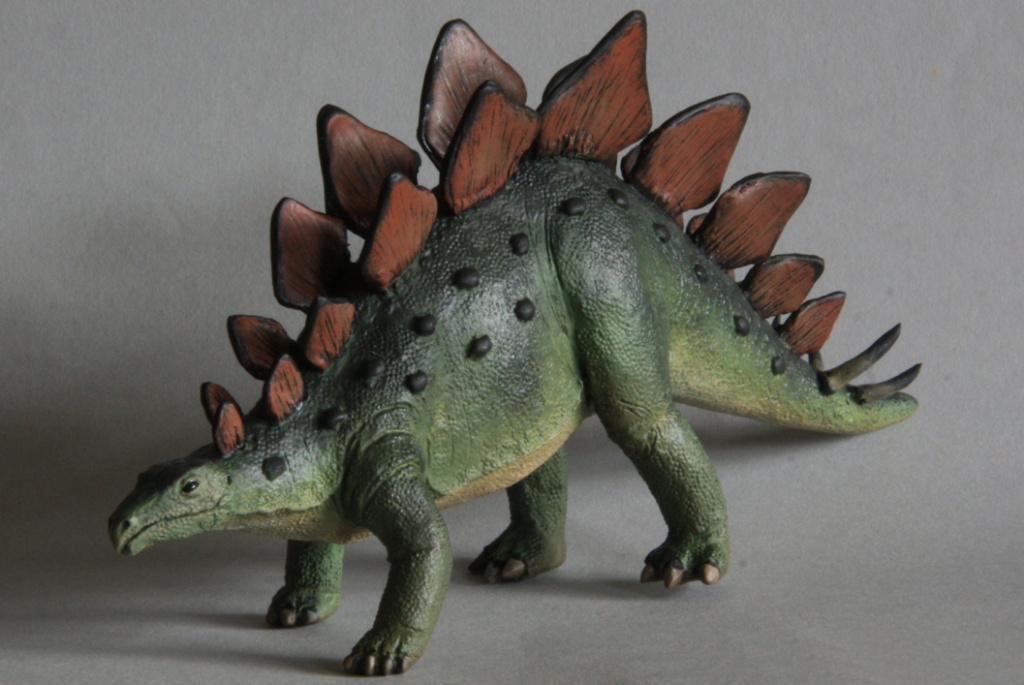
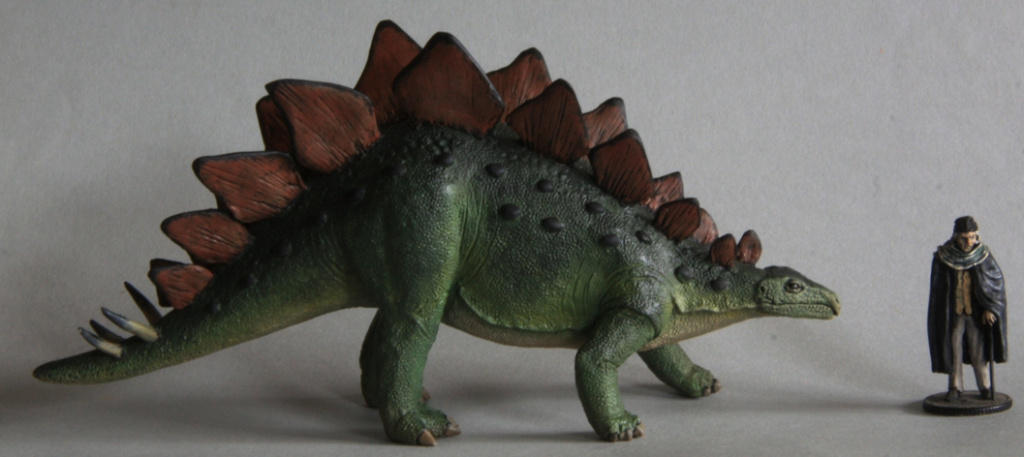
“They have never found a tail drag mark from Stegosaurus among the fossil footprints that cover the world, but as you know, that is how the scientists of yore thought the animals looked.”
The way we think each dinosaur looked might change with surprising frequency, but Andrew’s technique for making his models always remains the same. It combines a familiar approach of Green Stuff and wire armature with some special tricks he has developed to capture the uniqueness of these creatures who ruled the world for 165 million years.
“The bodies of my dinosaur models are all made with wire armature and Green Stuff. For Deinonychus, I fully sculpted it as a skeleton first, then muscles and so on until the feathered skin. Most of the work is lost under all that skin though.”
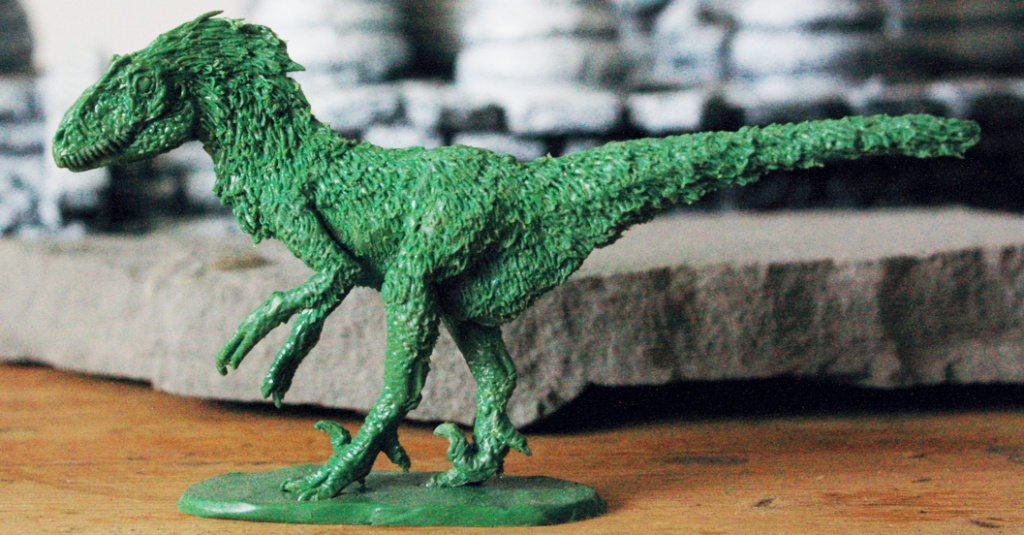
“There is a lot of sculpting involved. Diplodocus even in 1/48th scale is 22 inches long. It is made from Super Sculpey Polymer Clay, Milliput and Green Stuff, over a wire armature and a lump of foil to bulk out the fat belly.”
“I have made my own small tools for rendering scaly skin using flattened lumps of either Green Stuff or Milliput and peppering the surface with small holes. When pushed into soft modelling putty, they create a satisfying scaly texture. Diplodocus had poppy seeds in its skin too.”
Once sculpted, Andrew then paints his dinosaur models to stunning effect… but only when he has a suitable set of brushes. “We have very few art shops in my area of West Cornwall and I am very fussy about good quality brushes!”
“The one art shop we do have is a good 25 miles away and I rarely ever get the chance to go there. It is only ever open for a short space of time, on very few days as the the proprietor is getting on in years.”
Where Andrew is willing to deviate from his dedication to accuracy is by occasionally introducing people alongside his dinosaur models. Humans as we know them today were yet to walk the Earth when the dinosaurs were wiped out by an asteroid striking the Yucatan Peninsula in what is now Mexico some 66 million years ago.
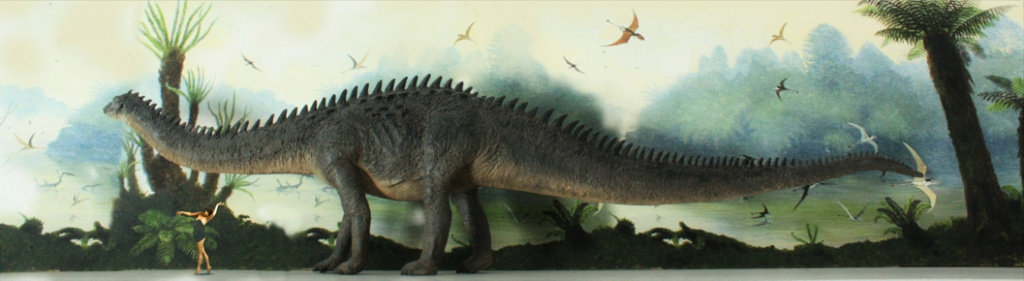
But Andrew will occasionally include 1:48 scale people he has sculpted alongside his dinosaurs for two reasons. The first is to give some idea of the sheer size of these animals. Whilst everyone knows Diplodocus was big, it is only when it is totally dwarfing a woman that you realise just how big.
The other reason for including people harks back to Andrew’s love of old movies starring dinosaurs, long before Spielberg defined what the modern-day blockbuster should look like.
“Inspired by the old monster films of cave men and dinosaurs having fights, I have often thought of warriors riding them and battling with each other and so on. The make for fine fantasy models and good artwork”
These warriors come from Andrew’s modular figures, made again from Green Stuff and wire armature. He sculpts both males and females and modifies the base as and when required, building characters to suit the project at hand.
“Doing the figures this way means I can spin off as many different characters as I wish. I just modify them, glue them together and dress them in whatever is required.”
“You can use the figures for any period in time or space, if you know what I mean.” Ah yes, another Doctor Who reference. “I once saw an illustration of a Silurian riding a dinosaur. I thought, one day, I could take that to another level.”
Watch this space.
Related Products
Related Articles
Modelling in a heat wave: Tips for using epoxy putty in hot weather
Epoxy modelling putty – Your guide to model making & sculpting putties
The real life snipers who fought ISIS immortalised in Magic Sculp
The benefits of mixing modelling putties
David Parker’s Crew School and bringing figures to life with the man himself
Meet the military modelling company with the Middle East at its heart